
For extraction systems with an air volume requirement above 50,000 m³/h, large industrial filter systems are used:
Battery filters - Extraction volume range between 50,000 and 100,000 m³/h
Line filters - Extraction volume range above 100,000 m³/h
Common characteristics
Energy-efficient system conception
Especially for industrial extraction systems with a large air volume requirement, the installation of the large filter systems close to the building is particularly important. This results in short distances for the extraction pipes and the return air system, which leads to lower pressure losses and makes a significant contribution to energy-saving operation.
Variety
The modular system of the filter program with several area rasters and different filter bags, variable in diameter and length, allows an optimal adaptation to each customer's requirement.
Safe construction
The individual modules of the filter housings are designed as self-supporting constructions and are made of galvanised sheet steel. The bent corner supports and the individual covering sheets are screwed together so that pressure-shock-resistant, internally smooth-walled filter system housings are created with the necessary stability even under high wind and snow loads. The filter units also comply with fire resistance class EW 90, so that they can be installed close to buildings.
Low flow resistance
The flow through the large industrial filter units has been optimised in order to reduce the internal resistance. The resulting low pressure losses between the inlet and outlet openings contribute to energy-saving operation.
Effective filter technology, return air operation
The high separation rate of the tested filter material used ensures a residual dust content in the return air of < 0.1 mg/m³, e.g. in the wood industry, so that the entire filtered extraction air can be returned to the workrooms via return air pipes or ducts. This direct return air mode massively reduces the energy requirement on the heating side and thus the use of fuel for firing in the boiler system.
The quality and equipment of the filter hoses are determined depending on the respective requirement.
Operatin mode
Industrial demands generally require multi-shift operation, so that the filter systems must be capable of continuous operation. This requirement can be met with the cleaning air system (process air) and compressed air (jet pulse system). Both processes ensure effective and at the same time gentle cleaning of the bag filters, so that long service lives can be achieved.
Large material quantities
The chips and dust separated in the filter systems are collected in containers or hoppers with built-in discharging devices and are transferred to a mechanical or pneumatic conveyor system via rotary valves.
The discharging systems used in the containers (fan wheels, chain conveyors or trough screws) are capable of conveying large quantities of material. When feeding material into the filter systems, care is taken to distribute it evenly over the individual filter system segments.
Energy-saving control technology
The control technology operates the system according to demand in order to achieve the greatest possible energy savings while at the same time providing a high level of operating comfort. The determining factors here are:
Speed control of the extraction fans via frequency converter for continuous adaptation of the extraction power to the extraction demand,
Optimised operation of the conveying systems using the possible material buffering in the containers of the filter systems,
Automatic opening and closing of the gate valves in the connection lines to the processing machines,
etc.






Compact filter systems
For extraction systems with an air volume requirement of up to 50,000 m³/h.
Download documents
SPÄNEX-large filter systems
Specific characteristics
Application
Battery filters are predestined for extraction systems with an air volume demand between 50,000 and 100,000 m³/h.
Construction
Battery filter units are assembled from the modules of the compact filter unit program. The battery filter plants consist of at least two or more units. Each unit consists of four modules:
- the sound-insulated fan cell with built-in centrifugal fan,
- the filter cell with the filter bags and the cleaning device,
- the container or hopper element, and
- the disposal unit.
Compactness
With the radial fans (negative pressure system) installed as standard in the fan cells, the battery filter systems represent complete extraction centers that require small installation areas for high performance.
Energy-efficient high-performance fans
Either one or more directly driven radial fans with efficiencies of more than 80 % are installed in the fan cells as standard, so that the power requirement is minimized from the outset. In conjunction with the standard IE3 (optionally IE4) efficiency class drive motors, a particularly high level of efficiency is achieved.
Effective filter and cleaning technology
The high separation rate of the tested filter material used ensures a minimized residual dust content in the return air, which is < 0.1 mg/m³ in the wood sector, for example. The quality and equipment of the filter material are determined depending on the respective task. The same applies to the cleaning method, whereby a choice is made between mechanical vibration and the compressed air cleaning jet pulse system. In the case of continuous operation of the extraction system and in the case of machining processes with a very high dust content, cleaning is carried out with compressed air (Jet-Pulse system). In the case of discontinuous operation of the extraction system, cleaning by mechanical vibration is also an option.
Even flow
The exhaust air is evenly distributed to the individual units of a battery filter system and the pipelines are connected to the individual units via flow-optimized inlet ducts.
This connection technique ensures a uniform material intake with a pre-separation effect of larger particles and a uniform inflow to the filter bags..
Quiet operation
The fan cells are lined with acoustic mats as standard and each is equipped with a silencer so that noise emissions are kept at a low level despite the high outputs. Additional sound damping devices are usually not required.



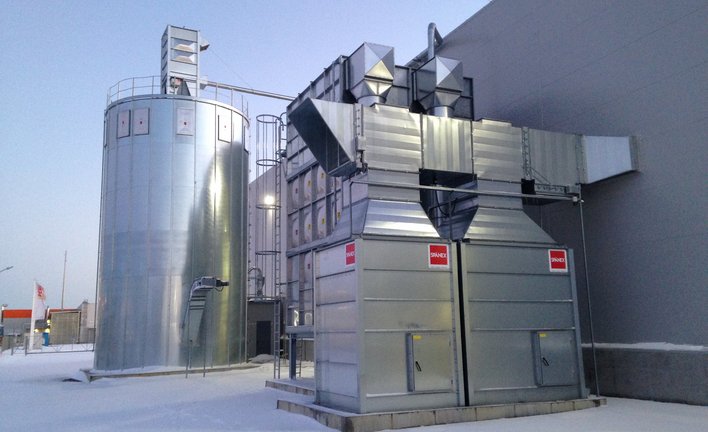





Compact filter systems
For extraction systems with an air volume requirement of up to 50,000 m³/h.
Download documents
SPÄNEX-large filter systems
Specific features
Application
In cases where large quantities of exhaust air are required, i.e. above 100,000 m³/h, line filter systems are used. This is the case, for example, in window factories and planing mills as well as in the furniture and plastics industry.
Construction
Line filter units are assembled from several units of the compact filter unit program. Each unit consists of four modules:
- the sound-insulated fan cell with built-in radial fans,
- the clean air chamber with the built-in cleaning device,
- the filter cell with the externally pressurized filter bags, and
- a container or hopper element for material intake with integrated
discharging device (fan wheel, chain conveyor or trough screw).
Depending on the amount of material, only the hopper element of the end unit or other intermediate units are each equipped with a pressure shock tested rotary valve, with which the separated chips and dust are transferred to a mechanical or pneumatic conveying device.
Variety, extensibility
By arranging several units in lines, filter systems of any size can be realized. Line filter systems for extraction volume flows of up to 200,000 m³/h are in use.
Line filter systems also offer the advantage of expandability, i.e., existing filter systems can be expanded by additional units and thus adapted to changed requirements..
Variants
The line filter systems are designed as a vacuum system as standard. In this case, the exhaust fans are installed in the fan cells. If required by the application, the exhaust fans can also be arranged outside the line filter systems, either downstream ("vacuum" system) or upstream ("overpressure" system).
The radial fans used in the vacuum systems achieve efficiencies of more than 80%. Efficiencies of up to 70 % are possible for fans on the raw air side.
Drive motors of efficiency class IE3 (optionally IE4) are used as standard to achieve a particularly high level of efficiency..
Effective filter technology
The high separation rate of the tested filter material used ensures a minimized residual dust content in the return air, which is < 0.1 mg/m³ in the wood sector, for example. The quality and equipment of the filter material are determined depending on the respective installation.
Cleaning
The line filter systems are mainly supplied with the so-called air cleaning system. In the air cleaning system, two radial fans mounted on a carriage are installed in the clean air chamber. These fans move from one row of bags to the next and blow the clean air drawn in into the filter bags. The flow reversal ensures effective and particularly gentle cleaning of the filter bags. Furthermore, the air cleaning convinces by its high operational reliability as well as the low operating costs, since only clean air is used for the cleaning of the filter bags.
Compressed air cleaning (Jet Pulse System) is only used for special applications.
Even flow
The extraction air is distributed evenly to the individual units of a line filter system, in which injection chambers are arranged between the units. The individual suction pipelines are connected to these injection chambers via non-return dampers. By reducing the speed and redirecting the flow, a pre-separation effect is created so that coarser particles are separated directly and the filter hoses are thus gently loaded only with fine particles and dust.
Quiet operation
The fan cells are lined with sound insulation mats as standard. In addition, a splitter sound damper is located inside the fan cells at each return air connection so that noise emissions are kept at a low level despite the high outputs. Additional external sound dampers are generally not required.
Several disposal options
The separated chips and dusts are collected in the containers of the individual units or in the common hopper and transferred via one or more pressure shock tested rotary valves to a mechanical or pneumatic conveying system, which conveys the material into one or more containers or into silos.
Pre-assembly in the factory
The individual modules of the units as well as the complete hopper with the discharging device (chain conveyor or trough screw) are pre-assembled in the factory in sizes suitable for transport , so that they only have to be assembled on site with the help of a crane. This results in short assembly times.







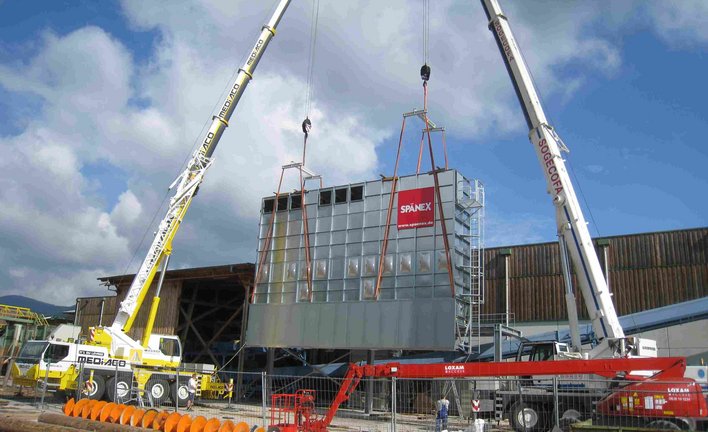

Compact filter systems
For extraction systems with an air volume requirement of up to 50,000 m³/h.
Download documents
SPÄNEX-large filter systems
Request now
Do you have any questions or other concerns? Simply fill in the form and we will take care of it.
Contact &
Consulting
We are always pleased to be there for you and to help you in the best possible way. Our business hours are Mon. - Thurs. from 07.30 to 16.30 and Fri. from 07.30 to 12.30.
Otto-Brenner-Straße 6
37170 Uslar